12/01/2023 - Oliver Hagenlocher - Press
埃马克开发集成制造解决方案:定制化的机器人应用确保了工件在生产中的快速流动
机器人自动化生产解决方案正在兴起:在它们的帮助下,可以在生产现场实现快速、低人工操作的工件流,从而降低单位成本,提高生产可靠性和质量。埃马克公司的例子说明了专业机械制造商是如何完成基础设计任务的:生产专家们将拾取机技术与高度个性化的机器人解决方案结合在一起,这些机器人解决方案经过精确设计,能够满足工件和生产工艺的要求。哪些细节是重要的?
图片:
根据国际机器人联合会(IFR)发布的《2022 年世界机器人技术》报告,目前全球约有 350 万台机器人用于工业生产。美国是全球三大机器人市场之一。埃马克公司的最新案例表明了这一点:专家们将高性能机器与不同的机器人单元相结合,不仅确保了机器上下料过程的高效率,还集成了质量检测、打标、清洁等附加工位。那么,埃马克使用机器人的首要目标是什么呢?"埃马克车削业务部负责人于尔根-迈尔解释说:"我们的重点始终放在工件的要求和相关的生产工艺上。"例如,决定性的问题是在一定时间内生产的批量大小,以及解决方案应如何自主工作。在任何情况下,我们都非常灵活,能够以多种方式适应现有的生产环境或空间条件"。
配有输送机、码垛机或抽屉
从细节上可以看出埃马克机器人解决方案的不同之处:例如,可以通过传送带、托盘、工件载体(如篮子),甚至散装物料来输送工件--在这些系统的帮助下,机器人在拾取新工件或放置加工好的工件时„“自行“操作”,因此每种解决方案都有不同的优势和基本条件。例如,如果要保证从上游生产方案到埃马克设备之间的零件流动顺畅,皮带或链板输送机就是一种理想的选择。机器人只需从传送带上拾取工件,然后再将工件放入传送带,根据空间情况或所需的工件流以不同的方式排列传送带。气动挡板可确保工件分离。还可以使用摄像头识别传送带上的工件角向。一个高度灵活的替代方案是所谓的无序拾取系统(“伸手到盒子里”)。在这里,工件处于混乱的位置,机器人手臂不仅在3D传感器系统的帮助下拾取工件,还可以正确识别和对准它们并将它们送入下一个加工工序。该系统可以灵活使用和配置多种应用。
相比之下,使用码垛机则需要 "有序 "启动:例如,使用篮筐手推车进行系统装载和卸载。它包含堆叠的篮子和相应的定位工装,其中放置零件,即每台车的工件数量相对较多,操作员只需将其推到规定的位置,机器人即可进入。装有成品工件的手推车位于另一个位置。"采用这种解决方案时,必须将埃马克机床的加工周期与期望的缓冲时间联系起来。因此,如果机床内的加工周期只有几秒钟,同时又想最大限度地减少机床上的操作人员,这种解决方案可能不合适,因为手推车将不得不过于频繁地更换。然而,这些正是我们为每个机器人解决方案进行的计算,并向客户提供相应的建议,"Maier 解释说。
第三种是通过抽屉系统装载:在这种情况下,工件通过气动驱动的抽屉被送入客户自己的工件托架中的机器人工作区。 在这种情况下,这些抽屉中的三个在一个柜中一个接一个地排列,允许在较小(可能的)占地面积内堆叠和处理更多的工件(中间无需操作员干预)。顺便提一下,上下料抽屉的过程并不会中断自动化流程-机器人只是继续在一个分隔的抽屉上工作。
埃马克机器人解决方案数量增加
以下内容适用于所有这些解决方案:单个机器人单元的设备选项非常广泛。例如,可以集成统计过程控制(SPC)。包括一个测量站。在这里,为了保证质量,单独的工件定期被送出、测量和重新放回。此外,测量站本身也可以集成到单元中,这样测量,包括测量机构对机器的反馈,都可以完全自动化。还可以在机器人单元内安装基于摄像头的检测系统、夹具更换系统(包括用于加工各种工件的夹具站)、小型清洗和清洁站、去毛刺系统或激光或雕刻站。各工位也由机器人进行装载和卸载。这样,工件就可以在不同的技术中连续流动。为了确保所有客户的持续成功,埃马克在规划自动化单元时依靠计算机模拟。专家们会检查大型生产线的周期时间、可达性、物料流和产量等因素。同样重要的是虚拟调试,即在生产线的数字孪生上测试流程和接口。这样就能在开发的早期阶段发现并消除不可预见的错误。更重要的是,"真实 "调试在以后的运行中会更快。
"Jürgen Maier 总结说:"总的来说,可以肯定的是,越来越多的机器人解决方案被应用到我们的机器上,这也是显而易见的。Jürgen Maier 总结道:"毕竟,我们有大量的机器已经采用了基于拾取技术的内部自动化。因此,我们可以相对容易地将这些解决方案集成到使用机器人的整体生产系统中,并在多种技术中建立起连续的零件流。因此,工件可以毫不费力地从A到达B,这意味着价值链上的人工操作不断减少。这就是我们的方法,它正在赢得越来越多客户的青睐。
联系人
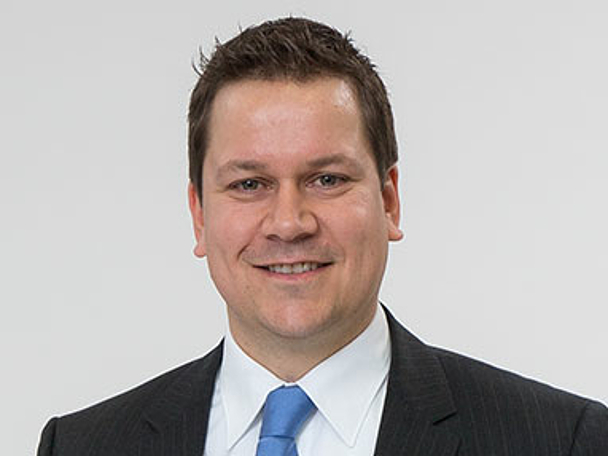